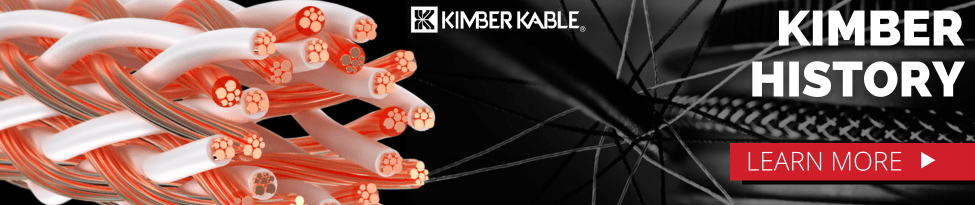
Back in 1979, it was pretty ground-breaking to be making any kind of specialist audio cable. Simon Dalton delves into Kimber's history to understand how they make such fine-sounding cables.
In 1979 the only cable company of any real note in the US was Monster cable - other, now mainstream, companies such as Audioquest and Cardas didn't appear on the scene until later (1980 and 1987 respectively). Ray Kimber developed Kimber Kable almost by accident following his research into reducing cable noise in pro applications (see my article in Connected magazine, issue 38). Pretty soon, though, word was spreading and the massive popularity of his 4PR speaker cable ensured legendary status from the start. As the American reviewer Neil Gader, writing in The Absolute Sound Buyers' Guide to Cables and Interconnects, puts it:
"Kimber Kable's 4PR was the defining entry-level cable for a generation of young audiophiles (including me) back in the early 1980s. Its distinctive brown/black braided design was my constant companion across a vast landscape of beginner systems. It's sound was honest and clean with no discernable tonal colorations to hijack an unwitting hobbyist. At that time it was the rare audiophile who didn't own a pair of 4PRs, and didn't keep them. I still have mine."
Being there from the start, especially with such a unique product, has ensured Kimber's place in the history of Hi-Fi. For decades now, Kimber has been a market leader in the field of audiophile cables; no mean feat in such a competitive market. Within that time many other companies have come and gone. So what is it that's kept them there?
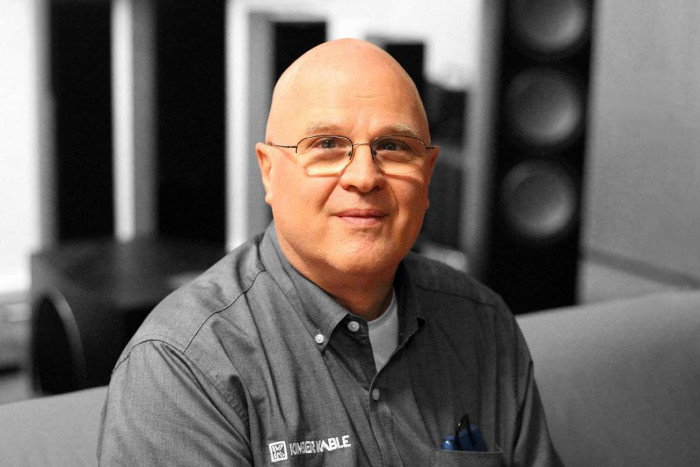
Ray Kimber
Reputation
The first, and probably most significant reason is the performance of Kimber's cables - and their resulting reputation. And it has been the ongoing research and development, based on sound scientific principles, which has secured and grown that reputation over the last 38 years.
In one sense, Kimber have adhered to that old adage "if it ain't broke, don't fix it". In other words, the basic principle at the heart of the woven cable design was correct back in 1979 and is still correct now, so why try to change it? Certainly not just so you can launch a 'new' product onto the market. Much as reviewers shy away from anything that hasn't been released in the last couple of years, Kimber have never been tempted to produce new products just to get the reviews. When a new cable does appear - such as the recent AXIOS range of headphone and USB cables - you can be sure it's the culmination of many years of experimentation and research, not simply a marketing driven desire to boost sales.
This is not to say that the cables haven't developed over that time. Over the years Ray has continued to test various metals as conductors, assorted manufacturing protocols, different stranding sizes, varying twist lengths and insulation, as well as methods for adhering insulation to cable; all the time improving, modifying, and expanding upon his original cable concept and design.
Neutrality and musicality
One of the reasons Kimber Kable had such a wide appeal was - and still is - its neutrality, meaning that it works well with a wide variety of systems. This is a reflection of Ray's desire to produce cables which let the character of the system they are being used on take centre-stage and letting the performance shine through, rather than imposing their own sound. In a recent interview with the online magazine StereoLife, Ray clarifies the point: "For me, the goal always was to have neutral electronics, neutral speakers and neutral cables.
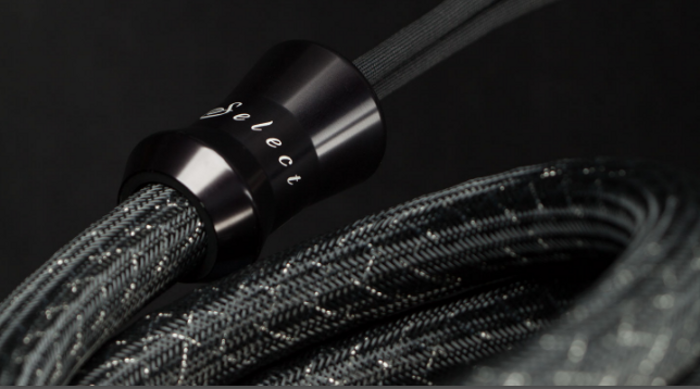
Kimber Select speaker cable
This goal of producing cables which allow the natural character of your audio components to determine the sound signature is reflected in a review of one of Kimber's flagship cables, their Select KS-6068 speaker cable. Neil Gader, reviewing for The Absolute Sound magazine, said of the cable:
"With a tonal balance that's predominately neutral, the KS's overall personality--though not invisible--isn't hard to nail down. And rightly so, as it promptly assumes the character of the system it's immersed in. So, whether your audio rig is strictly grainfree photorealistic or gauzily impressionistic, that's what Kimber is going to give you in return".
Attention to detail
One aspect that certainly counts towards Kimber's longevity is the attention to detail they give when designing and manufacturing products - it's a way of ensuring that anything that reaches the customer reflects the ongoing values of the brand and the high quality standards that Ray demands. Perhaps an example would help.
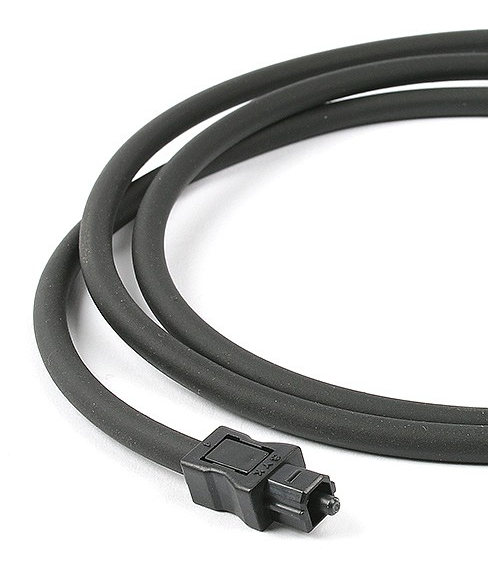
Kimber's OPT-1 digital optical cable was introduced in the early 1990s and has remained pretty well unchanged in design even since. The primary reason for this was the time spent initially developing the cable to make sure it would be as good as it possibly could be.
They first sourced a company who made an extremely pure optical fibre for laparoscopic tools. Having bought thousands of meters of the fibre, and a specialist machine to cut it, they found the resulting performance was good but not up to the standard they demanded from such high
quality cable.
This didn't make sense; the cable was of such a high standard but the sound performance didn't match and there was no way they were going to sell a cable they weren't happy with (regardless of how much they had invested in it). There had to be an explanation. Kimber investigated further and discovered that the heat that was generated when applying insulation to the cable was damaging the sound performance. The solution? Develop a completely new way of applying the insulator at a lower temperature, solving the issue and finally achieving the performance they always thought the cable was capable of!
Then there was the issue of termination. Most optical cables on the market used polished connectors on each end of the cable, and it was this type of connection that Kimber used on their prototype. However, after much experimentation with these connections, Kimber found that the gloss surface had the effect of reflecting some of the light from the cable. This is not especially problematic where an optical cable is used for medical applications, but in the audio sphere the data loss that this light leakage creates is obviously going to affect the final sound.
Kimber therefore switched to a matt black connector, which doesn't look as attractive but solved the problem and ultimately sounds better (ironically, the cable was reviewed by one of the leading US magazines who concluded that it was a lot better than the others they'd tried but complained that the connectors were rather crude, whilst the others were shiny!).
This one example is typical of Kimber's approach to manufacturing. It's the same reason that, although it's time consuming, their silver cable is fed by hand onto bobbins in preparation for braiding, so it can go through a final check for imperfections before being woven. That attention to detail ensures that Kimber keep their status and, more importantly, ensures that customers get the very best product.
Click here to shop Kimber Kable